ارتباط نوع پوشش لوله با حفاظت کاتدی
جلوگیری از خوردگی در سازه های زیرزمینی نیاز به ترکیبی از پوشش بادوام و حفاظت کاتدی دارد. هزینه حفاظت کلی شامل هزینه پوشش و سیستم حفاظت کاتدی می شود. انتخاب پوشش لوله مناسب می تواند به طور قابل توجهی بر هزینه حفاظت کاتدی تأثیر بگذارد. هزینه سیستم حفاظت کاتدی به مقاومت الکتریکی پوشش مورد استفاده روی لوله مربوط می شود. مقاومت به مشخصات الکتریکی پوشش، مساحت کل سطح فولاد و میزان آسیب پوشش بستگی دارد. جریان الکتریکی مورد نیاز برای محافظت از خط لوله با گذشت زمان برای همه پوشش ها بالا می رود. پوشش هایی با کمترین نیاز به جریان اولیه و حداکثر پایداری (یعنی کمترین میزان تغییر در نیاز جریان در طول زمان) هزینه نصب و راه اندازی سیستم حفاظت کاتدی را به حداقل می رساند. میزان جریان الکتریکی موردنیاز به طور قابل توجهی با توجه به مقاومت خاک، دما، محیط شیمیایی خط لوله و نوع پوشش لوله در خطوط لوله متفاوت است.
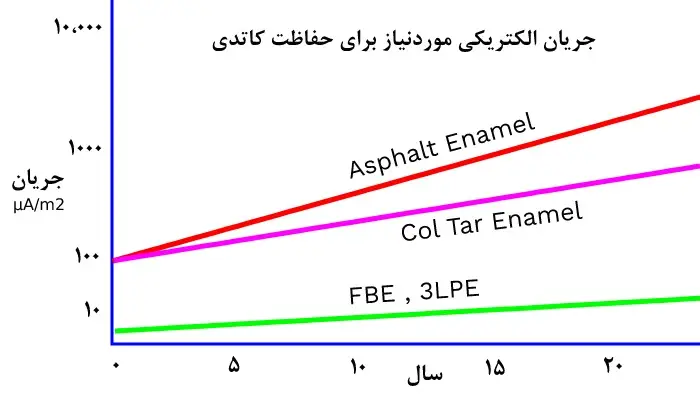
جریان الکتریکی موردنیاز برای حفاظت کاتدی به نوع پوشش لوله بستگی دارد و در طول زمان افزایش می یابد
ویژگیهای پوشش FBE لوله
از زمانی که برای اولین بار در سال ۱۹۶۰ پوشش اپوکسی معرفی شد، FBE تک لایه قابلیت خود را به عنوان پوشش خط لوله ثابت کرده است، اکنون پوشش لوله اپوکسی رایج ترین پوشش خط لوله در آمریکای شمالی است و طرفداران زیادی در بقیه جهان دارد. این پوشش لوله نه تنها دارای ویژگی های عملکردی مهم برای اجرا در انواع عملیات ساخت و ساز است، بلکه عملکرد ثابت شده ای در حفاظت از سیستمهای زیرزمینی و زیردریایی دارد. ثابت شده است که عملکرد پوشش FBE برای خطوط لوله، اتصالات و سرجوشها موثر است.
ویژگیهای مهم زیر سبب شده است که مواد اپوکسی با پیوند همجوشی به عنوان یک گزینه مطلوب در صنعت پوشش لوله مطرح شود.
۱- چسبندگی عالی به سطح فولاد تمیز
۲- مقاومت شیمیایی خوب
۳- نفوذپذیری کم اکسیژن
۴- سازگار با حفاظت کاتدی
۵- مقاوم در برابر ترک خوردگی تنشی
۶- مقاومت در برابر عوامل بیولوژیکی
۷- سخت، اغلب در زیر دریا، در مناطق صخره ای، کوهستانی، در بیابان و قطب شمال نصب می شود.
۸- مقاومت عالی در برابر نفوذ
۹- مقاومت خوب در برابر ضربه، آسیب ضربه محدود به نقطه تماس است.
۱۰- آسیب قابل مشاهده است و به راحتی تعمیر می شود.
۱۱- مقاومت بالا در برابر سایش
۱۲- انعطاف پذیری خوب
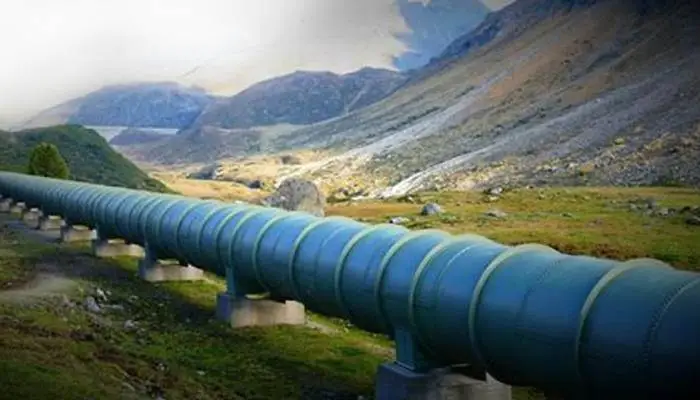
خط لوله پوشش شده با پوشش FBE دولایه
پوشش FBE دولایه
پوشش دولایه FBE در اوایل دهه ۱۹۹۰ معرفی شد که قابلیت های بیشتری را نسبت به پوشش FBE تک لایه ارائه می دهد. پوشش دولایه اپوکسی از اعمال یک لایه اضافی پوشش FBE بر روی پوشش پایه اپوکسی بدست می آید. لایه بالایی به طور معمول، اما نه لزوما، در مرحله مذاب (پیش ژل) بر روی لایه اولیه رسوب می کند. نتیجه یک پیوند شیمیایی سازگار بین دو لایه است. مزیت قابل توجه فناوری چند لایه این است که ویژگی های منحصر به فرد را می توان با انتخاب لایه های مختلف پوشش با ویژگی های خاص توسعه داد. در پوشش دولایه FBE، هر لایه به گونهای طراحی شده است که ویژگیهای خاصی را ارائه دهد که با هم ترکیب میشوند تا نتایج عملکردی را تولید کنند که به طور قابلتوجهی از نتایج یک پوشش فراتر میرود. برای استفاده این پوشش در خط لوله، لایه زیرین به عنوان پوشش خوردگی طراحی شده است و اغلب همان ماده ای است که به عنوان یک FBE مستقل استفاده می شود. درک این نکته مهم است که تفاوت های عملکردی قابل توجهی بین پوشش های تجاری موجود وجود دارد. توسعه انواع پوشش های FBE بصورت یکسان انجام نمی شود.
لایه بالایی سیستم پوشش FBE دولایه برای کاربردهای خاصی مانند ضد لغزش (سطح ناهموار، اصطکاک بالا)، مقاومت در برابر اشعه ماوراء بنفش (UV)، مقاوم در برابر دمای بالا و مقاومت در برابر آسیب در طول احداث خط لوله، طراحی می شود.
پوشش دولایه FBE مزایای بیشتری نسبت به پوششهای پیچشی دور لوله دارد. از طریق افزایش بهره وری و استفاده نسبتاً کم مواد، پوشش دولایه اپوکسی، یک گزینه اقتصادی بشمار می رود. خطوط لوله اولیه از پوشش FBE تک لایه با ضخامت تا دو میلی متر استفاده می کردند. در حالی که این ضخامت بالا هنوز هم در بعضی موارد خاص موردنیاز است اما معمولاً ضخامت بین ۶۵۰ تا ۱۰۰۰ میکرومتر کافی خواهد بود. مطالعات آزمایشگاهی بر روی پوشش دولایه FBE بهبود قابل توجه مقاومت در برابر آسیب را با این ضخامت نشان داد این یک بهبود قابل توجه در برابر ضربه در مقایسه با یک پوشش FBE تک لایه با همان ضخامت است.
اجرای پوشش دولایه FBE
اجرای پوشش دولایه FBE بر روی لوله های فولادی، یک فرآیند ساده است که این خود یکی از نقاط قوت این پوشش لوله بشمار می رود. مانند بسیاری از سیستمهای پوششدهی دیگر، ابتدا سطحی که قرار است پوشش داده شود، تمیز و آماده سازی میشود تا بستر مناسب برای افزایش چسبندگی ایجاد شود. سپس لوله تا دمای کاربری مورد نیاز گرم می شود. گرمایش ممکن است به روشهای مختلفی از جمله القایی یا برخورد مستقیم با شعله انجام شود. پس از رسیدن به دمای موردنظر، FBE از طریق فرآیند اسپری الکترواستاتیکی بر روی لوله پاشش می شود. پودر اپوکسی سپس ذوب میشود و روی سطح فلز جریان مییابد که در نتیجه یک روکش صاف و سخت ایجاد میشود. برای سیستمهای دو لایه، مجموعه دومی از نازلها، لایه پوشش بالایی را بلافاصله بعد از لایه اولیه اعمال میکند. پوشش دولایه FBE به سرعت پخت می شود و می تواند پس از چند ثانیه وزن لوله را تحمل کند. به عبارت دیگر چنانچه لوله پوشش شده با پوشش اپوکسی دولایه در یک سطح صاف قرار گیرد، لایه پوشش شده زیر لوله بقدری سخت و محکم است که در برابر وزن لوله استحکام و مقاومت کافی را دارد. پس از پخت پوشش، برای جابجایی ایمن لوله، فرآیند خنک کاری انجام می شود، سپس لوله بازرسی می شود و در صورت لزوم تعمیر می شود. بعد از این مرحله، لوله پوشش داده شده برای انتقال به سایت خط لوله و نصب آماده است. برخی از مزایای این روش اجرا عبارتند از حذف VOCs یا موارد آلی فرار در فرایند پوشش دهی و تقریباً حذف ضایعات است (به عنوان مثال، اسپری بیش از حد به راحتی بازیابی می شود).
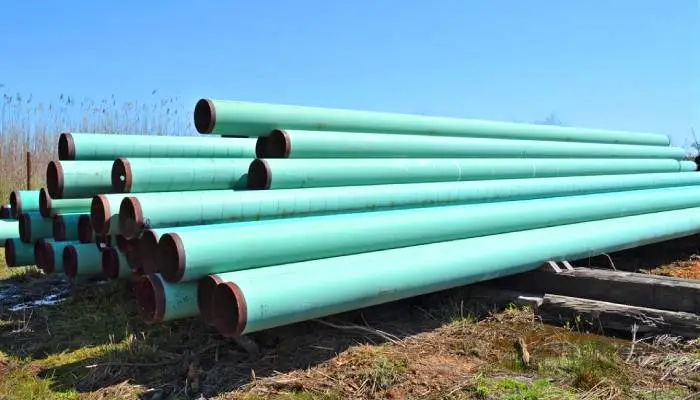
پوشش دو لایه اپوکسی محافظ خوردگی و مقاوم در برابر صدمات خارجی
تجربه میدانی پپوشش FBE دولایه
آسیب های ناشی از حمل و نقل به طور قابل توجهی در مقایسه با آنچه که معمولاً برای پوشش FBE تک لایه در طول مسیر انتقال از کارخانه پوشش دهی تا محل احداث خط لوله اتفاق می افتد، کاهش یافته است. جوش های گیره نیز با سیستم FBE دو لایه پوشانده شدند. این فرآیند بیشتر از برنامه FBE تک لایه وقت گیر نیست.
برای تطبیق خط لوله با عوارض زمین، در طول مسیر احداث آن، خمیدگی های زیادی وجود داشت. در مناطق سردسیر شمالی در حین ساخت، تنها ۱۴ ترک پوشش در تعداد کل ۲۹۶۰ خم وجود داشت این مشکل در نقاطی بوجود آمده بود که در آنها شواهدی از خم شدن بیش از حد وجود داشت. در مناطق گرمتر مسیر خط لوله، هیچ ترک پوششی پس از خمش گزارش نشده است. محل ترک ها با برس پاک سازی شده و با یک مایع چند جزئی به ضخامت ۵۰۰ میکرومتر پوشانده شدند. از آن زمان به بعد برای جلوگیری از مشکلاتی از این دست، لایه بالایی پوشش FBE دولایه، برای افزایش انعطاف پذیری بهبود داده است.
سیستمهای پوشش FBE دولایه مدتهاست که مزایای خود را در زمینههای تخصصی، از جمله مقاومت در برابر اشعه ماوراء بنفش، افزایش اصطکاک و خطوط لوله با دمای بالا نشان دادهاند. پروژه خط لوله رودخانه کرن در سال ۲۰۰۳ با استفاده از این فناوری، پیشرفت چشمگیری را در مقاومت در برابر آسیب های ناشی از حمل و نقل لوله و احداث خط لوله نشان داد.