پوشش اپوکسی ۱۰۰٪ جامد
پوششهای اپوکسی ۱۰۰٪ جامد و فاقد حلال شامل رزین اپوکسی (یا اپوکسی اصلاح شده یا اپوکسی نووالاک)، عامل پخت (کیورینگ) رنگدانه، کاتالیست، پرکنندهها و حجم دهندهها و عامل جریان پذیری می باشد. مهمترین رزین اپوکسی در پوششهای FBE بر پایه بیس فنل A و شناخته شده ترین آن دیگلیسیدیل اتر بیس فنل A یا (DGEBA) و معروفترین عوامل پخت (هاردنر) دیآمینهای آروماتیک و آلیفاتیک هستند.
از ویژگیهای بارز پوشش های FBE می توان درجه بالای چقرمگی یا سختی، اتصالات عرضی بسیار محکم و گسترده، قابلیت چسبندگی بسیار بالا به سطح، مقاومت بالای دمایی و مقاومت شیمیایی مطلوب در برابر انواع واکنشگرهای شیمیایی را نام برد. مهمترین معیار ارزیابی پوششهای داخلی محافظ خوردگی، بطور عام، مقاومت شیمیایی، مقاومت دمایی و میزان انعطافپذیری میباشد. از خصوصیات ممتاز پوششهای FBE تنوع این پوششها جهت سازگاری با شرایط متفاوت محیطی و دماهای مختلف بهره برداری است. از این جهت بسته به نیازهای ویژه هر پروژه می توان از پوشش FBE خاص و متناسب با شرایط خط لوله از نظر دما، فشار و محیط شیمیایی استفاده کرد. در محیط گاز ترش غالبا یک لایه نازک آستری پایه فنولیک نیز اعمال می شود. رزینهای فنولیک نتیجه واکنش شیمیایی بین فنل و فرمالدئید هستند. پرایمر فنولیک علاوه بر تقویت چسبندگی پوشش اصلی، مقاومت پوشش را در برابر تاول زدگی نیز تقویت می کند.
کنترل کیفیت پوششهای FBE نیز متناسب با شرایط محیطی حاکم بر خط لوله جهت گیری پیدا می کند. آزمونهای عمومی پوششها مانند مقاومت در برابر سایش، جدایش کاتدی، ضربه، نفوذ اجسام صلب، نفوذ آب در دمای بالا و چسبندگی در این استانداردها درنظر گرفته شده اند. اما در حضور گاز ترش آزمونهای مربوط به مقاومت شیمیایی پوشش مانند آزمون اتوکلاو و آزمون مه نمکی نیز مطرح می شود. روش تست اتوکلاو به عنوان یکی از مهمترین آزمونهای صحه گذاری کیفیت پوششها در محیط گاز ترش بیان شده است.
آزمون اتوکلاو با شبیه سازی شرایط محیطی خط لوله از نظر دما، فشار و محیط شیمیایی (در دو یا سه فاز مایع، گاز و هیدروکربنی) با درجه اطمینان بالایی تناسب پوششهای داخلی را برای محیطهای خاص گاز ترش ارزیابی می کند. طراحی هر فاز بر مبنای ویژگیهای خط لوله و گونه های شیمیایی موجود انجام می شود. گازهای H₂S و CO₂ می توانند در دما و فشار بالا به داخل ساختار پوشش نفوذ نمایند. در صورتیکه با برداشته شدن سریع فشار گاز در انتهای آزمون اتوکلاو، گازها قادر به خروج از پوشش نباشند، پوشش تاول خواهد زد. سرعت تقلیل فشار بایستی بر مبنای شدیدترین تغییرات فشار در خط لوله طراحی شود. ارزیابی پوشش پس از آزمون اتوکلاو شامل بررسی چشمی تاول زدگی، تورم پوشش و نیز مقایسه چسبندگی پوشش در هر فاز قبل و بعد آزمون، آزمون منفذیابی و یا حتی بررسی تغییر سختی پوشش میباشد. بنابراین پوشش داخلی خط لوله گاز ترش بایستی ویژگیهایی افزون بر مشخصات فنی متعارف پوششهای سطح خارجی خطوط لوله داشته باشد. مقاومت در برابر نفوذ گازها و یونها، مقاومت در برابر تغییرات شدید pH و مقاومت دمایی بالا در این زمره قرار می گیرند. عدم توجه به پیشنیازها و الزامات کیفی یک پوشش قبل از کاربری در محیط گاز ترش معمولاً فاجعه بار است به عنوان نمونه در سالیان اخیر پوششدهی داخلی خط لوله "56 انتقال گاز ترش آیگات 6 به روش پوشش دوجزیی مایع به این دلیل که اولاً، پوششهای دوجزیی مایع ابداً مناسب تماس با گاز ترش با مشخصات شیمیایی میادین پارس جنوبی نیستند و ثانیاً، پوشش مذکور فاقد هرگونه تجربه و پشتوانه عملی در موارد مشابه بود، با شکست کامل مواجه شد. متأسفانه آثار زیانبار این شکست علیرغم پیشبینی اولیه هنوز بر صنعت انتقال گاز کشور سایه افکنده است.
برای روش شدن مطلب نتیجه آزمون اتوکلاو بر روی پوششهای اپوکسی مایع دوجزئی و پوشش FBE در دو مقطع زمانی ولی با شرایط محیطی کاملا یکسان در دمای ۸۵ درجه سانتیگراد، فشار سیال ۱۰۳ بار، نوع سیال آب دیونیزه، دوره آزمون ۷ روز و تقلیل فشار نهایی سریع در فاز آبی و گازی به شرح زیر می باشد:
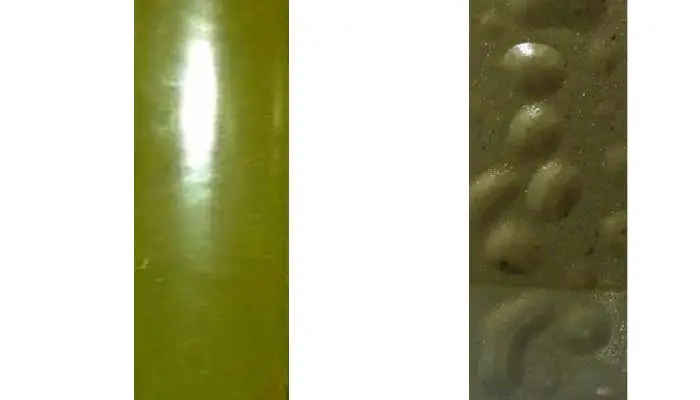
آزمون اتوکلاو پوشش اپوکسی؛ پوشش داخلی اپوکسی مایع (راست) و پوشش داخلی FBE (چپ)
پوشش اپوکسی مایع دوجزئی: تغییر چسبندگی از B به D همراه با تغییر رنگ و تاول زدگی گسترده و بزرگ که در آزمون مردود شد.
پوشش FBE: چسبندگی بدون تغییر، رنگ بدون تغییر، بدون تاول زدگی و نتیجه نهایی قبول
نتیجه این آزمون نشان می دهد که پوشش اپوکسی مایع یا پوشش رنگ اپوکسی دوجزئی باید با ضخامت بالایی بین ۲ تا ۳ برابر پوششهای FBE اعمال شود. ضخامت بالا به طور معمول انعطاف پذیری پوششهای سخت را کاهش می دهد. تجربه میدانی در مورد پوشش اپوکسی مایع Protegole 130-HT نشان داد که:
۱- پوشش رنگ اپوکسی در موارد متعدد حتی قادر به تحمل تنشهای الاستیکی حین جابجایی و حمل و نقل لولههای پوشش شده نبود.
۲- نفوذ گاز در پوششهای اپوکسی مایع دوجزئی ضمن ایجاد تاولهای بزرگ در تمام سطح باعث آماس و تورم پوشش تا ۴۰٪ نسبت به ضخامت اولیه شده است.
۳- نتیجه آزمون به وضوح زایل شدن چسبندگی پوشش اپوکسی مایع به سطح را نشان می دهد. چسبندگی پوشش به سطح پس از آزمون اتوکلاو از شروط تایید پوشش می باشد.
۴- تغییر رنگ پوشش به شرطی که کوقت و سطحی نباشد می تواند دلیلی بر تغییر ساختار فیزیکی یا شیمیایی پوشش در تماس با محیط خورنده باشد.
اجرای پوشش داخلی FBE
پس از اجرای مراحل تمیزکاری و بلاستینگ سطح داخلی، آستری فنولیک با ضخامت حدود ۲۵ میکرون در سطح لوله اعمال می شود. پس از آن لوله و اتصالات باید در کورههای مخصوص پیش گرم شوند. این مرحله از تولید در تعیین کیفیت محصول نهایی بسیار حائز اهمیت است. یکنواختی دما در تمام سطح لوله و یا اتصالات در یک محدوده دمایی خاص که غالبا کمتر از ۲۰۰ درجه سانتیگراد نیست و پیشگیری از هرگونه آلودگی سطح مانند آلودگی هیدروکربنی در نتیجه عملیات حرارتی از شروط لازم پیش گرمی است.
غالبا برای اطمینان از یکنواختی توزیع گرما در سطح لوله از ترمومترهای لیزری که در فرکانس بالا دمای لوله را دریافت و به نرم افزار مخصوص پوشش لوله Pipe Protection ارسال می کنند، استفاده می شود. این سیستم بصورت آنلاین دمای تمام نقاط سطح را توسط چارتهای بلادرنگ در اختیار بخش کنترل کیفیت قرار می دهد تا از پوشش دهی لوله هایی که بطور یکنواخت گرما دهی نشده اند جلوگیری شود.
پوششهای FBE پس از مرحله پیش گرمی و تثبیت دمای سطح در محدوده موردنظر متناسب با ابعاد و شکل لوله با ضخامت حدود ۲۵۰ میکرون بر روی سطح داخلی لوله اعمال می شوند. غالب پوششهای FBE نیازمند طی عملیات حرارتی پس گرمی به منظور پخت هستند. بنابراین از کوره های پخت با قابلیت کنترل پروفایل دمایی جهت پخت کامل این پوشش ها بهره گرفته می شود صحت این مرحله نیز اهمیت بسزایی در کیفیت محصول نهایی دارد. پس از خنک کاری لوله ها و یا اتصالات تا دمای محیط بوسیله دمش هوا و یا جریان آب، بازرسی های کنترل کیفیت پوشش از جمله ضخامت سنجی، کنترل چسبندگی و آزمون منفذیابی نیز به اجرا گذاشته می شود. در اینجا مدیریت زمان در اجرای موفق عملیات پوشش دهی داخلی لوله نقش ارزنده ای دارد. آزمون آنالیز حرارتی به کمک روش گرماسنجی پیمایش تفاضلی معتبرترین روش تعیین میزان پخت پوشش و یکی از آزمونهای مهم در تعیین کیفیت پوشش محسوب می شود.
پوشش FBE سرجوش لوله
سرجوش ها (Field Joints) آسیب پذیرترین نقاط در یک خط لوله به شمار می روند. همسنگ نبودن قابلیتهای فنی پوشش در محل سرجوشها نسبت به پوشش اصلی و محدودیتهای کیفی اجرای پوشش محل سرجوشها در محل اجرای پروژه همواره به عنوان چالش مجریان خطوط لوله مطرح بوده است. بطور معمول دو سر لوله ها و یا اتصالات جوشی در خطوط تولید با فاصله مشخصی که کات بک گفته می شود، پوشش دهی نمی شوند.
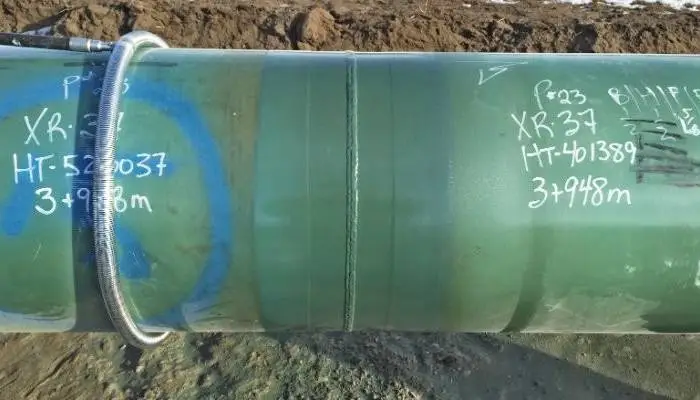
پوشش FBE سرجوش لوله
از طرف دیگر کارایی یک پوشش داخلی محافظ خوردگی، خصوصاً در یک خط لوله انتقال گاز ترش بطور اساسی به یکپارچگی پوشش در سراسر خط لوله وابسته است. سامانه های رباتیک امروزه به خوبی فرآیندهای آماده سازی سطح، اعمال پوشش و کنترل کیفیت پوشش محل سرجوشها را انجام می دهند. این سیستمها از ترکیب چند دستگاه در یک قالب و یا در قالبهای جداگانه ابتدا سطح داخلی محل سرجوشها را از نظر تمیزی و زبری مناسب آماده نموده و سپس با همان سیستم پوششی بدنه خط لوله، محل سرجوشها را پوششدهی می نمایند و در نهایت با انجام آزمونهای های منفذیابی و ضخامت سنجی، صحت اجرای پوششدهی را ارزیابی می کنند. کوپلینگهای پیش ساخته پوشش شده نیز با پیشینه ای بالغ بر ۳۰ سال به خوبی جوابگوی نیازهای فنی یک خط لوله انتقال گاز ترش هستند. این کوپلینگ ها که در سطح داخلی محل سرجوشها مابین دو لوله قرار میگیرند، همسنگ با پوشش اصلی خط لوله، پوششدهی می شوند و همراه با نوعی ماستیک مقاوم در برابر حرارت، محدوده پوشش نشده دو سر لوله را در برگرفته و در طول کاربری خط لوله، آنرا در مقابل خوردگی مصون نگه می دارند. این کوپلینگهای پیش ساخته هم برای اقطار پایین و هم اقطار بالای خطوط لوله مورد استفاده قرار می گیرند.
پوشش داخلی FBE خط لوله گاز ترش
افت فشار سیال در خطوط لوله گاز با عامل اصطکاک نسبت مستقیم دارد. بنابراین تقلیل زبری سطح منجر به کاهش نیروی اصطکاک و نهایتاً کاهش افت فشار سیال می گردد.
مطالعات گسترده در خصوص تأثیر پوششهای داخلی در کاهش افت فشار، نشان می دهد که پوششهای داخلی FBE یکی از بهترین پوششهای بهبود دهنده جریان سیال می باشند که بسته به مشخصات سیال و خط لوله، افت فشار را تا ۳۰٪ و گاه بیشتر و هزینه های سرمایه گذاری و بهره برداری ایستگاه های تقویت فشار را به میزان قابل توجهی کاهش می دهند. نقش پوششهای داخلی در خطوط لوله با فشار بالا مانند خطوط انتقال گاز در مقایسه با خطوط لوله با فشار پایین از جمله خطوط انتقال آب پررنگتر و اقتصادی تر می باشد. صافی فوق العاده سطح پوششهای داخلی FBE منافع دیگری را نیز به همراه دارد. از جمله ترسیب جرم، هیدراتها، مواد آلی، واکس و پارافین و نظیر آنها را که وابسته به انرژی و ساختار پروفایل سطح است، حذف و یا محدود می شود و از این طریق عملیات بازرسی سطح داخلی خط لوله و یا پیگ رانی هم از نظر اجرایی و هم از نظر زمانی بهبود می یابد.انتخاب پوشش داخلی بر پایه درک کامل شرایط، آزمونهای آزمایشگاهی و تجربه استوار است. بنابراین شناخت خوردگی در محیط گاز ترش از یک طرف و قابلیتهای فنی پوشش از طرف دیگر، آگاهی از سوا بق و پشتوانه بین المللی و نتایج قابل قبول آزمایشگاهی، پیشنیازهای اساسی یک سیستم پوششی در محیط گاز ترش است. پوشش های FBE با پیشینه ای نزدیک به ۵۰ سال و قریب سه دهه سابقه درخشان کاربری در محیط گاز ترش گزینه ای ایده آل به شمار می روند. اعمال پوششهای خاص داخلی FBE ساده ترین گزینه و استفاده توامان با فولاد آلیاژی مخصوص گاز ترش در لوله ها مؤثرترین روش جهت کنترل خوردگی است. این پوششها عمر مفید سازه های فولادی و از جمله خطوط لوله را از طریق کنترل نرخ خوردگی، که در برخی منابع حداقل ۲ برابر عنوان شده است، افزایش می دهند. از طرف دیگر با کاهش میزان اصطکاک سیال و سطح داخلی لوله، باعث تقلیل نرخ افت فشار و نهایتاً بهبود جریانپذیری سیال میگردند. بهبود جریان سیال متناسب با مشخصات فنی آن، قطر خط لوله و میزان صافی سطح پوشش تا ۳۰٪ گزارش شده است. بهبود جریانپذیری سیال به نوبه خود هزینه های مربوطه به برپایی ایستگاههای تقویت فشار و انرژی را بطور محسوس کاهش می دهد. بر مبنای آنچه تاکنون گفته شد می توان
استنباط کرد اجرای پوششهای داخلی FBE در خطوط لوله انتقال گاز ترش صرفنظر از اینکه جنس خط لوله از فولاد آلیاژی مخصوص می باشد یا کربن استیل، امری ضروری است.
منافع متعدد میان مدت و بلندمدت پوششهای داخلی FBE و هزینه ناچیز ۱ تا ۳ درصدی اجرای این پوششها در مقایسه با قیمت لوله های کربن استیل (و نه حتی از جنس فولاد آلیاژی)، تغییر رویکرد صنعت نفت و گاز را به سمت استفاده هر چه بیشتر از این پوششها در پی داشته است.